Son yıllarda yeni enerji endüstrisinin hızlı gelişimi sayesinde lazer kaynağı, hızlı ve istikrarlı avantajları nedeniyle tüm yeni enerji endüstrisine hızla nüfuz etmiştir. Bunların arasında lazer kaynak ekipmanı, tüm yeni enerji endüstrisindeki uygulamaların en yüksek oranını oluşturmaktadır.
Lazer kaynakYüksek hızı, geniş derinliği ve küçük deformasyonu nedeniyle hayatın her kesiminde kısa sürede ilk tercih haline geldi. Nokta kaynaklarından alın kaynaklarına, yapı ve sızdırmazlık kaynaklarına kadar,lazer kaynakbenzersiz hassasiyet ve kontrol sağlar. Askeri sanayi, tıbbi bakım, havacılık, 3C otomobil parçaları, mekanik sac, yeni enerji ve diğer endüstriler dahil olmak üzere endüstriyel üretim ve imalatta önemli bir rol oynamaktadır.
Diğer kaynak teknolojileriyle karşılaştırıldığında lazer kaynağının kendine özgü avantajları ve dezavantajları vardır.
Avantajı:
1. Hızlı hız, büyük derinlik ve küçük deformasyon.
2. Kaynak normal sıcaklıkta veya özel koşullar altında yapılabilir ve kaynak ekipmanı basittir. Örneğin, bir lazer ışını elektromanyetik alanda sürüklenmez. Lazerler vakum, hava veya belirli gaz ortamlarında kaynak yapabildikleri gibi, camdan geçen veya şeffaf olan malzemeleri de lazer ışınına kaynak yapabilirler.
3. Titanyum ve kuvars gibi refrakter malzemeleri kaynaklayabilir ve aynı zamanda farklı malzemeleri de iyi sonuçlarla kaynaklayabilir.
4. Lazer odaklandıktan sonra güç yoğunluğu yüksektir. En boy oranı 5:1'e ulaşabilir ve yüksek güçlü cihazlarda kaynak yapılırken 10:1'e kadar çıkabilir.
5. Mikro kaynak yapılabilir. Lazer ışını odaklandıktan sonra küçük bir nokta elde edilebilir ve doğru bir şekilde konumlandırılabilir. Otomatik seri üretim elde etmek için mikro ve küçük iş parçalarının montajına ve kaynağına uygulanabilir.
6. Ulaşılması zor alanlara kaynak yapabilir ve büyük bir esneklikle temassız uzun mesafe kaynak yapabilir. Özellikle son yıllarda YAG lazer işleme teknolojisi, lazer kaynak teknolojisinin daha yaygın olarak tanıtılmasını ve uygulanmasını sağlayan fiber optik iletim teknolojisini benimsemiştir.
7. Lazer ışınının zamana ve mekana göre bölünmesi kolaydır ve birden fazla ışın aynı anda birden fazla yerde işlenebilir, bu da daha hassas kaynaklama için koşullar sağlar.
Kusur:
1. İş parçasının montaj doğruluğunun yüksek olması gerekir ve kirişin iş parçası üzerindeki konumu önemli ölçüde saptırılamaz. Bunun nedeni, odaklama sonrasında lazer noktası boyutunun küçük olması ve kaynak dikişinin dar olması, dolgu metali malzemelerinin eklenmesini zorlaştırmasıdır. İş parçasının montaj doğruluğu veya kirişin konumlandırma doğruluğu gereksinimleri karşılamıyorsa kaynak kusurlarının oluşması muhtemeldir.
2. Lazerlerin ve ilgili sistemlerin maliyeti yüksektir ve tek seferlik yatırım büyüktür.
Yaygın lazer kaynak kusurlarılityum pil üretiminde
1. Kaynak gözenekliliği
Yaygın kusurlarlazer kaynakgözeneklerdir. Kaynak eriyik havuzu derin ve dardır. Lazer kaynak işlemi sırasında nitrojen erimiş havuza dışarıdan girer. Metalin soğuması ve katılaşması sırasında sıcaklığın düşmesiyle azotun çözünürlüğü azalır. Erimiş havuz metali kristalleşmeye başlayacak kadar soğuduğunda çözünürlük keskin bir şekilde ve aniden düşecektir. Bu sırada büyük miktarda gaz çökelerek kabarcıklar oluşturacaktır. Kabarcıkların yüzme hızı metalin kristalleşme hızından düşükse gözenekler oluşacaktır.
Lityum pil endüstrisindeki uygulamalarda, gözeneklerin özellikle pozitif elektrotun kaynağı sırasında oluşmasının muhtemel olduğunu, ancak negatif elektrotun kaynaklanması sırasında nadiren meydana geldiğini görüyoruz. Bunun nedeni pozitif elektrotun alüminyumdan, negatif elektrotun ise bakırdan yapılmış olmasıdır. Kaynak sırasında iç gaz tamamen taşmadan yüzeydeki sıvı alüminyum yoğunlaşarak gazın taşması ve irili ufaklı delikler oluşturması engellenir. Küçük stomalar.
Gözeneklerin yukarıda belirtilen nedenlerine ek olarak, gözenekler ayrıca dış hava, nem, yüzey yağı vb. içerir. Ayrıca nitrojenin üfleme yönü ve açısı da gözeneklerin oluşumunu etkileyecektir.
Kaynak gözeneklerinin oluşumunun nasıl azaltılacağına gelince?
İlk olarak, daha öncekaynakGelen malzemelerin yüzeyindeki yağ lekeleri ve yabancı maddelerin zamanında temizlenmesi gerekir; Lityum pillerin üretiminde gelen malzeme denetimi önemli bir süreçtir.
İkincisi, koruyucu gaz akışı kaynak hızı, güç, konum vb. faktörlere göre ayarlanmalı ve ne çok büyük ne de çok küçük olmalıdır. Koruyucu pelerin basıncı lazer gücü ve odak konumu gibi faktörlere göre ayarlanmalı, ne çok yüksek ne de çok düşük olmalıdır. Koruyucu pelerin ağızlığının şekli, koruyucu pelerin kaynak alanını eşit şekilde kaplayabilecek şekilde kaynağın şekline, yönüne ve diğer faktörlere göre ayarlanmalıdır.
Üçüncüsü, atölyedeki havanın sıcaklığını, nemini ve tozunu kontrol edin. Ortam sıcaklığı ve nem, alt tabakanın yüzeyindeki nem içeriğini ve koruyucu gazı etkileyecektir ve bu da erimiş havuzda su buharının oluşumunu ve kaçışını etkileyecektir. Ortam sıcaklığı ve nemi çok yüksekse, alt tabakanın yüzeyinde ve koruyucu gazda çok fazla nem olacak, bu da büyük miktarda su buharı üreterek gözeneklere neden olacaktır. Ortam sıcaklığı ve nemi çok düşükse, alt tabakanın yüzeyinde ve koruyucu gazda çok az nem olacak, bu da su buharı oluşumunu azaltarak gözenekleri azaltacaktır; kalite personelinin kaynak istasyonundaki sıcaklık, nem ve toz hedef değerini tespit etmesini sağlayın.
Dördüncüsü, lazer derin nüfuzlu kaynakta gözenekleri azaltmak veya ortadan kaldırmak için ışın salınımı yöntemi kullanılır. Kaynak sırasında salınımın eklenmesi nedeniyle, kirişin kaynak dikişine ileri geri salınımı, kaynak dikişinin bir kısmının tekrar tekrar erimesine neden olur, bu da sıvı metalin kaynak havuzunda kalma süresini uzatır. Aynı zamanda kirişin sapması birim alan başına ısı girdisini de arttırır. Kaynağın derinlik-genişlik oranı azalır, bu da kabarcıkların ortaya çıkmasına yardımcı olur ve böylece gözenekler ortadan kalkar. Öte yandan, kirişin salınımı küçük deliğin de buna göre salınmasına neden olur, bu da kaynak havuzu için bir karıştırma kuvveti sağlayabilir, kaynak havuzunun konveksiyonunu ve karışmasını artırabilir ve gözeneklerin ortadan kaldırılmasında faydalı bir etkiye sahip olabilir.
Beşincisi, darbe frekansı, darbe frekansı, lazer ışınının birim zaman başına yaydığı darbe sayısını ifade eder; bu, erimiş havuzdaki ısı girişini ve ısı birikimini etkileyecek ve daha sonra erimiş havuzdaki sıcaklık alanını ve akış alanını etkileyecektir. havuz. Darbe frekansı çok yüksekse, erimiş havuza aşırı ısı girdisine yol açarak erimiş havuzun sıcaklığının çok yüksek olmasına neden olur, metal buharı veya yüksek sıcaklıklarda uçucu olan diğer elementler üretilerek gözeneklerin oluşmasına neden olur. Darbe frekansı çok düşükse, eriyik havuzunda yetersiz ısı birikmesine neden olacak, eriyik havuzunun sıcaklığının çok düşük olmasına neden olacak, gazın çözünmesi ve kaçması azalacak ve gözenekler oluşacaktır. Genel olarak konuşursak, darbe frekansı, alt tabaka kalınlığına ve lazer gücüne bağlı olarak makul bir aralıkta seçilmeli ve çok yüksek veya çok düşük olmaktan kaçınılmalıdır.
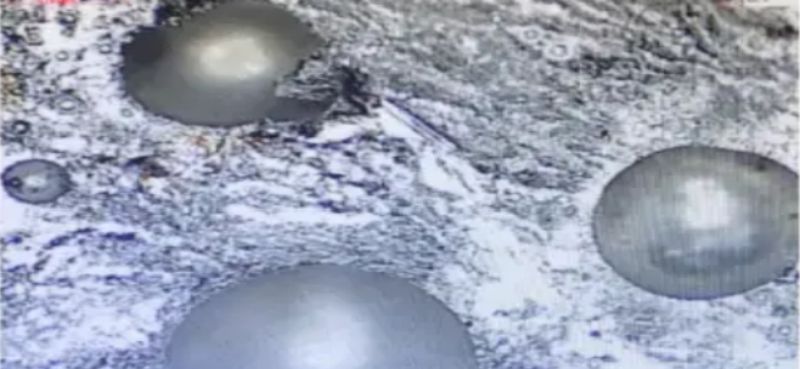
Kaynak delikleri (lazer kaynağı)
2. Kaynak sıçraması
Lazer kaynağında kaynak işlemi sırasında oluşan sıçrama, kaynağın yüzey kalitesini ciddi şekilde etkileyecek, merceği kirletecek ve zarar verecektir. Genel performansı şu şekildedir: Lazer kaynağı tamamlandıktan sonra malzemenin veya iş parçasının yüzeyinde birçok metal parçacık belirir ve malzeme veya iş parçasının yüzeyine yapışır. En sezgisel performans, galvanometre modunda kaynak yaparken, galvanometrenin koruyucu merceğinin bir süre kullanılmasından sonra yüzeyde yoğun çukurların oluşması ve bu çukurların kaynak sıçramasından kaynaklanmasıdır. Uzun bir süre sonra ışığı engellemek kolaylaşır ve kaynak ışığında sorunlar yaşanır, bu da kaynak bozulması ve sanal kaynak gibi bir dizi soruna neden olur.
Sıçramanın nedenleri nelerdir?
Birincisi, güç yoğunluğu, güç yoğunluğu ne kadar büyük olursa sıçramanın üretilmesi de o kadar kolay olur ve sıçrama doğrudan güç yoğunluğuyla ilişkilidir. Bu asırlık bir sorundur. Sektör en azından şu ana kadar sıçrama sorununu çözemedi ve sadece bir miktar azaldığını söyleyebiliriz. Lityum pil endüstrisinde, pil kısa devresinin en büyük suçlusu sıçramadır, ancak temel nedeni çözememiştir. Sıçramanın akü üzerindeki etkisi ancak koruma açısından azaltılabilir. Örneğin, kaynak parçasının çevresine toz giderme portlarından oluşan bir daire ve koruyucu kapaklar eklenir ve sıçramanın etkisini ve hatta aküye zarar gelmesini önlemek için daireler halinde sıra sıra hava bıçakları eklenir. Kaynak istasyonu etrafındaki çevreye, ürün ve bileşenlere zarar vermenin araçları tükettiği söylenebilir.
Sıçrama probleminin çözümüne gelince, sadece kaynak enerjisinin azaltılmasının sıçramanın azalmasına yardımcı olduğu söylenebilir. Penetrasyonun yetersiz olması durumunda kaynak hızının azaltılması da yardımcı olabilir. Ancak bazı özel proses gereksinimlerinde çok az etkisi vardır. Aynı işlemdir, farklı makineler ve farklı malzeme grupları tamamen farklı kaynak efektlerine sahiptir. Bu nedenle, yeni enerji endüstrisinde yazılı olmayan bir kural vardır: tek bir ekipman için tek bir kaynak parametresi seti.
İkincisi, işlenen malzemenin veya iş parçasının yüzeyi temizlenmezse yağ lekeleri veya kirletici maddeler de ciddi sıçramalara neden olacaktır. Şu anda en kolay şey işlenmiş malzemenin yüzeyini temizlemektir.
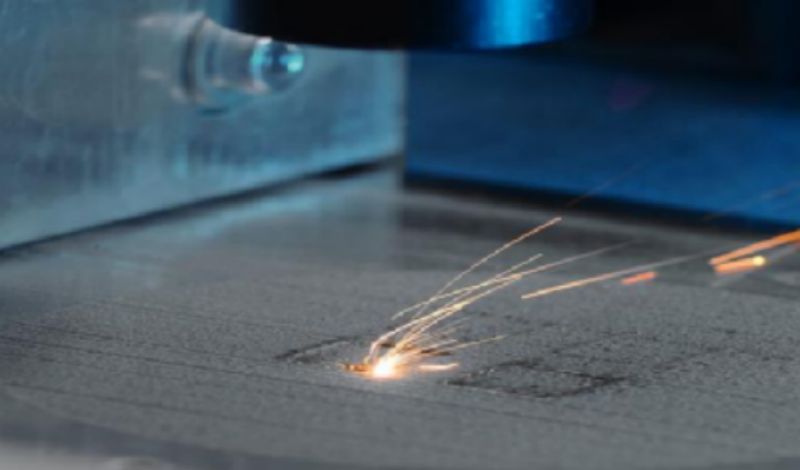
3. Lazer kaynağının yüksek yansıması
Genel olarak konuşursak, yüksek yansıma, işleme malzemesinin küçük bir dirence, nispeten pürüzsüz bir yüzeye ve yakın kızılötesi lazerler için düşük bir emme oranına sahip olduğu ve bu da büyük miktarda lazer emisyonuna yol açtığı ve çoğu lazerin kullanıldığı anlamına gelir. dikey Malzeme veya az miktarda eğim nedeniyle, geri dönen lazer ışığı çıkış kafasına yeniden girer ve geri dönen ışığın bir kısmı bile enerji ileten fibere bağlanır ve fiber boyunca içeriye doğru iletilir. Lazerin içindeki çekirdek bileşenlerin yüksek sıcaklıkta olmaya devam etmesini sağlar.
Lazer kaynağı sırasında yansımanın çok yüksek olması durumunda aşağıdaki çözümler alınabilir:
3.1 Yansıma önleyici kaplama kullanın veya malzemenin yüzeyini işleyin: kaynak malzemesinin yüzeyinin yansıma önleyici bir kaplama ile kaplanması, lazerin yansıtıcılığını etkili bir şekilde azaltabilir. Bu kaplama genellikle lazer enerjisini geri yansıtmak yerine emen, düşük yansıtıcılığa sahip özel bir optik malzemedir. Akım toplayıcı kaynağı, yumuşak bağlantı vb. gibi bazı işlemlerde yüzeye kabartma da yapılabilmektedir.
3.2 Kaynak açısını ayarlayın: Kaynak açısını ayarlayarak lazer ışınını kaynak malzemesine daha uygun bir açıyla vurabilir ve yansıma oluşumunu azaltabilirsiniz. Normalde, lazer ışınının kaynak yapılacak malzemenin yüzeyine dik olarak gelmesi yansımaları azaltmanın iyi bir yoludur.
3.3 Yardımcı emici eklenmesi: Kaynak işlemi sırasında, kaynağa belirli miktarda toz veya sıvı gibi yardımcı emici eklenir. Bu emiciler lazer enerjisini emer ve yansımayı azaltır. Özel kaynak malzemelerine ve uygulama senaryolarına göre uygun emicinin seçilmesi gerekir. Lityum pil endüstrisinde bu pek olası değildir.
3.4 Lazeri iletmek için fiber optik kullanın: Mümkünse, yansımayı azaltmak için lazeri kaynak konumuna iletmek için fiber optik kullanılabilir. Optik fiberler, kaynak malzemesinin yüzeyine doğrudan maruz kalmayı önlemek ve yansıma oluşumunu azaltmak için lazer ışınını kaynak alanına yönlendirebilir.
3.5 Lazer parametrelerinin ayarlanması: Lazer gücü, odak uzaklığı ve odak çapı gibi parametrelerin ayarlanmasıyla lazer enerjisinin dağılımı kontrol edilebilir ve yansımalar azaltılabilir. Bazı yansıtıcı malzemeler için lazer gücünün azaltılması yansımaları azaltmanın etkili bir yolu olabilir.
3.6 Bir ışın ayırıcı kullanın: Bir ışın ayırıcı, lazer enerjisinin bir kısmını emme cihazına yönlendirebilir, böylece yansımaların oluşmasını azaltabilir. Işın bölme cihazları genellikle optik bileşenlerden ve soğuruculardan oluşur ve uygun bileşenlerin seçilmesi ve cihazın yerleşiminin ayarlanmasıyla daha düşük yansıtma elde edilebilir.
4. Kaynak alt kesimi
Lityum pil üretim sürecinde hangi süreçlerin eksik kesmeye neden olma olasılığı daha yüksektir? Alttan kesme neden oluşur? Hadi analiz edelim.
Alt kesim, genellikle kaynak hammaddeleri birbirleriyle iyi bir şekilde birleştirilmemiştir, boşluk çok büyüktür veya oluk görünür, derinlik ve genişlik temel olarak 0,5 mm'den büyüktür, toplam uzunluk kaynak uzunluğunun %10'undan büyüktür veya Ürün proses standardından istenen uzunluktan daha büyük.
Lityum pil üretim sürecinin tamamında, alttan kesmenin meydana gelme olasılığı daha yüksektir ve genellikle silindirik kapak plakasının sızdırmazlık ön kaynağı ve kaynağında ve kare alüminyum kabuk kapak plakasının sızdırmazlık ön kaynağı ve kaynağında dağıtılır. Bunun ana nedeni, sızdırmazlık kapak plakasının Kaynak için kabuk ile birlikte çalışması gerektiğidir; sızdırmazlık kapak plakası ile kabuk arasındaki eşleştirme işleminin aşırı kaynak boşluklarına, oyuklara, çökmeye vb. eğilimli olması, dolayısıyla alttan kesmelere özellikle eğilimli olmasıdır. .
Peki alttan kesmeye ne sebep olur?
Kaynak hızı çok hızlıysa, kaynağın merkezine işaret eden küçük deliğin arkasındaki sıvı metalin yeniden dağıtılması için zaman kalmayacaktır, bu da kaynağın her iki tarafında da katılaşmaya ve alttan kesmeye neden olacaktır. Yukarıdaki durum göz önüne alındığında kaynak parametrelerini optimize etmemiz gerekiyor. Basitçe söylemek gerekirse, çeşitli parametreleri doğrulamak için tekrarlanan deneylerdir ve uygun parametreler bulunana kadar DOE yapmaya devam edilir.
2. Kaynak malzemelerindeki aşırı kaynak boşlukları, oyuklar, çökmeler vb. boşlukları dolduran erimiş metal miktarını azaltacak ve alttan kesmelerin meydana gelme olasılığını artıracaktır. Bu bir ekipman ve hammadde meselesidir. Kaynak hammaddelerinin prosesimizin gelen malzeme gereksinimlerini karşılayıp karşılamadığı, ekipmanın doğruluğunun gereksinimleri karşılayıp karşılamadığı vb. Normal uygulama, tedarikçilere ve ekipmandan sorumlu kişilere sürekli işkence yapmak ve dövmektir.
3. Lazer kaynağının sonunda enerji çok hızlı düşerse, küçük delik çökebilir ve bu da yerel alttan kesmeye neden olabilir. Güç ve hızın doğru şekilde eşleştirilmesi, alttan kesmelerin oluşmasını etkili bir şekilde önleyebilir. Eski deyişte olduğu gibi deneyleri tekrarlayın, çeşitli parametreleri doğrulayın ve doğru parametreleri bulana kadar DOE'ye devam edin.
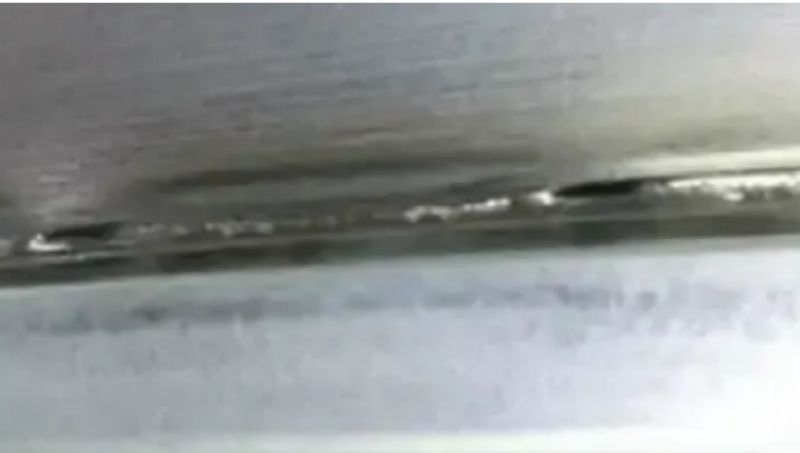
5. Kaynak merkezinin çökmesi
Kaynak hızı yavaşsa, eriyik havuzu daha büyük ve geniş olacak ve erimiş metal miktarı artacaktır. Bu, yüzey geriliminin korunmasını zorlaştırabilir. Erimiş metal çok ağırlaştığında kaynağın merkezi batabilir ve çukurlar ve çukurlar oluşabilir. Bu durumda, eriyik havuzunun çökmesini önlemek için enerji yoğunluğunun uygun şekilde azaltılması gerekir.
Başka bir durumda kaynak aralığı, delinmeye neden olmadan sadece bir çökme oluşturur. Bu şüphesiz ekipmanın presle oturmasıyla ilgili bir sorundur.
Lazer kaynağı sırasında oluşabilecek kusurların ve farklı kusurların nedenlerinin doğru anlaşılması, herhangi bir anormal kaynak sorununun çözümünde daha hedefe yönelik bir yaklaşıma olanak sağlar.
6. Kaynak çatlakları
Sürekli lazer kaynağı sırasında ortaya çıkan çatlaklar çoğunlukla kristal çatlakları ve sıvılaşma çatlakları gibi termal çatlaklardır. Bu çatlakların ana nedeni, kaynağın tamamen katılaşmadan önce oluşturduğu büyük büzülme kuvvetleridir.
Lazer kaynağında çatlakların aşağıdaki nedenleri de vardır:
1. Mantıksız kaynak tasarımı: Kaynağın geometrisinin ve boyutunun uygun olmayan tasarımı, kaynakta stres yoğunlaşmasına ve dolayısıyla çatlaklara neden olabilir. Çözüm, kaynak stresi yoğunlaşmasını önlemek için kaynak tasarımını optimize etmektir. Uygun ofset kaynakları kullanabilir, kaynak şeklini değiştirebilirsiniz, vb.
2. Kaynak parametrelerinin uyumsuzluğu: Çok yüksek kaynak hızı, çok yüksek güç vb. gibi kaynak parametrelerinin yanlış seçilmesi, kaynak alanında eşit olmayan sıcaklık değişikliklerine yol açarak büyük kaynak gerilimine ve çatlaklara neden olabilir. Çözüm, kaynak parametrelerini belirli malzeme ve kaynak koşullarına uyacak şekilde ayarlamaktır.
3. Kaynak yüzeyinin kötü hazırlanması: Kaynak öncesinde kaynak yüzeyinin uygun şekilde temizlenmemesi ve oksitlerin, gresin vb. uzaklaştırılması gibi ön işlemlerin yapılmaması, kaynağın kalitesini ve mukavemetini etkileyecek ve kolayca çatlaklara yol açacaktır. Çözüm, kaynak alanındaki yabancı maddelerin ve kirletici maddelerin etkili bir şekilde arıtılmasını sağlamak için kaynak yüzeyinin yeterince temizlenmesi ve ön işleme tabi tutulmasıdır.
4. Kaynak ısı girişinin yanlış kontrolü: Kaynak sırasında aşırı sıcaklık, kaynak katmanının uygun olmayan soğuma hızı vb. gibi kaynak sırasında ısı girişinin zayıf kontrolü, kaynak alanının yapısında değişikliklere yol açarak çatlaklara neden olur. . Çözüm, aşırı ısınmayı ve hızlı soğumayı önlemek için kaynak sırasında sıcaklığı ve soğuma hızını kontrol etmektir.
5. Yetersiz gerilim giderme: Kaynak sonrası yetersiz gerilim giderme işlemi, kaynaklı alanda yetersiz gerilim gidermeye neden olacak ve bu da kolayca çatlaklara yol açacaktır. Çözüm, kaynak sonrası ısıl işlem veya titreşim işlemi gibi uygun gerilim giderme işleminin uygulanmasıdır (ana neden).
Lityum pillerin üretim sürecine gelince, hangi süreçlerin çatlaklara neden olma olasılığı daha yüksektir?
Genellikle silindirik çelik kabukların veya alüminyum kabukların sızdırmazlık kaynağı, kare alüminyum kabukların sızdırmazlık kaynağı vb. gibi sızdırmazlık kaynağı sırasında çatlaklar oluşmaya eğilimlidir. Ayrıca modül paketleme işlemi sırasında akım toplayıcının kaynağı da eğilimlidir. çatlaklara.
Elbette bu çatlakları azaltmak veya yok etmek için dolgu teli, ön ısıtma veya başka yöntemler de kullanabiliriz.
Gönderim zamanı: Eylül-01-2023